 Meet Adam Wolf, co-founder of Wayne and Layne, a company that makes open source nerdery. In MAKE Volume 28, Adam wrote about making a Van de Graaff generator from a soda can and co-wrote (along with MAKE’s John Baichtal) an article on making a wireless arcade-quality joystick-and-button-panel for playing video games. I asked Adam my standard get-to-know-a-geek questions. Here’s what he had to say: Tell us a bit about yourself. I live in Minneapolis, MN. I recently switched from working at a large defense contractor to a small engineering design services company. I get to do a lot of fun stuff with Linux and microcontrollers. On nights and weekends, I'm half of Wayne and Layne, LLC, an open source hardware electronics kit business. We've done a few jobs on commission, but mostly we just think of cool things, make them, and then sell them for enough money to slowly grow while sending us to Maker Faires around the United States and letting us buy new tools and things to experiment with. When I'm not doing that, I'm usually reading or watching improv at our friendly local community theater with my wife. Why do you like making things? It’s easy to be philosophical about this, and talk about “the manifestation of human will outside the body” but pragmatically, making things is full of joy. It’s enjoyable to have an idea and then go through with it, in any creative form. There's a sense of success after overcoming obstacles encountered during the practice of a skill. It's fun to see yourself getting better at something. I like making toys, and it's fun to see someone’s eyes light up when they “get it” working with an exhibit or toy you made. Can you tell us something about the two projects you made for MAKE? I made two projects for MAKE Volume 28. The first is a Bluetooth Arcade Controller. This project has a long, long history. I shared a dorm with Matthew, the other half of Wayne and Layne, during college and we had a Gauntlet arcade cabinet. We made a new control panel with more buttons and cup holders, and put a computer on the inside. Don't worry folks, the electronics were toast — no working cabinets were harmed! The cabinet was huge, like a big refrigerator. I still live in an apartment, and there's no room for a huge arcade cabinet, but there’s nothing like playing old video games on big arcade-style controls that you can really beat up. Matthew had done some experiments with Bluetooth keyboards for Wayne and Layne, to create the heart of a wireless, apartment-friendly arcade console. This project was on our list for years and years, without really going anywhere. Jeff Rowberg ran into his post and had us do some work for him related to his Keyglove Kickstarter project. Jeff later pointed us towards a nicer Bluetooth keyboard module. At the same time, John Baichtal was kicking around ideas with me to do an article for an upcoming issue of MAKE. This provided the impetus for Matthew and I to finish the electronics, and John did a bang up job making a cool enclosure out of MicroRAX and acrylic. Matthew and I sourced parts and had some PCBs produced, so folks can buy a Bluetooth Arcade Controller kit from Maker Shed, put it on their Arduino Mega, attach a bunch of buttons and joysticks, and build their own wireless arcade controller. It connects to your computer and looks like a regular wireless keyboard, so there's no drivers to mess around with. The only configuration is to configure the games to take the appropriate keypresses. We brought one to World Maker Faire in New York this year and paired it with an Android tablet. People had tons of fun playing games with it. The second project is a simple electrostatic generator. While I'm pretty confident with my electronics skills, I don't really have much mechanical know-how. I’ve been deliberately doing stretch projects to help learn and practice these skills. One wintry weekend in Minneapolis, I ran across a picture online of a Van De Graaff machine with a pop can for the top collector. They claimed they were able to get sparks out of it, and I was instantly taken back to childhood electrostatic projects in my parents’ basement. Pretty much all of those ended without any sparks due to a lack of funding and hands-on experience. After picking up a variety of parts at Ax-Man, a local surplus store, my wife and I started working on an improvised Van De Graaff machine. I took it to a hackerspace, and it drew enough of a crowd I decided to document the build. It's definitely a step in a new direction for me–there isn't a single chip in the whole project! What kind of thing do you dream of making? I have a long list of projects where the only thing stopping me from doing them is time, but they’re relatively grounded. I went through a few years where I had to consciously avoid thinking about wearable computing or risk spending the rest of that week daydreaming and writing prose and code about how enabling wearable computing would be. The “quantified self” movement is intensely interesting to me and I know I’ll be making something awesome in that area, eventually. However, right now, my biggest dream is to make a toy that’s fun and inspirational. It should occasionally surprise the person playing with it, and help inspire people to make things themselves. I have a pet theory that if enough people practice the skills, become capable, and think of themselves as makers, it'll have a beneficial "herd immunity" effect across society. I'd like to help that. Oh, and space. I'd love to build something that goes into space. Can you tell us about one of your favorite tools? Excluding computers, Linux, Python, and the Internet, I’m going to say checklists and tables. When I'm in the thick of it, and really struggling with a problem, I like to make a table of all the possibilities and work through them. I need a framework to be methodical, and tables and checklists seem to do the trick. The New Yorker ran an article a few years ago called "The Checklist" that made me try incorporating more checklists into my life. There was one time I was working with a tricky bootloader that used to fit just fine in 2k, but the compiler had changed since then, and there were some small changes I wanted to make. On top of that, there were different fuse settings to use. I floundered for a while, and really started to despair about the success of the project. I opened up a Google doc, made a spreadsheet, listed out all the options I knew of for each of the variables, and started compiling and flashing. It wasn't long before I had found a working combination that did what it should. What are you working on now?
The photo above is what I’ve been working on this week, a version of our latest kits, the “Blinky POV” and “Blinky Grid” which are simple reprogrammable LED toys. The grid is 56 LEDs in a rectangle, and it can scroll text or simple graphics and animations, and the Blinky POV is a persistence of vision toy that you swing through the air, and the LEDs blink fast enough that it paints an image through the air. The cool part about these kits is that they are reprogrammed by going to our website, entering the text or drawing the graphic in our webpage, holding the light sensors to your monitor or smartphone, and pressing the program button on the webpage. There are two squares on the website that blink black and white, and through their blinking, transmits the new program to the kit. They’re one of my favorite things that Matthew and I have ever created — I taught a summer camp of 70 or so 12- and 13-year-old girls how to solder using the ones that we currently have available for sale. The ones in the photo are surface mount versions of that kit. We’ve gone through every step of the process to make it as simple as possible to surface mount solder these kits, and they’re designed to be displayed as badges. They’ll come preprogrammed with the message “I can solder SMD!” Photos by Amanda Nix MAKE Volume 28, Toys & Games! MAKE Volume 28 hits makers’ passion for play head-on with a 28-page special section devoted to Toys and Games, including a toy “pop-pop” steamboat made from a mint tin, an R/C helicopter eye-in-the-sky, and a classic video game console. You’ll also build a gravity-powered catapult, a plush toy that interacts with objects around it, and a machine that blows giant soap bubbles. Play time is a hallmark of more intelligent species– so go have some fun! On newsstands now! Buy or Subscribe David Lang, something of a reluctant maker, is on a journey, intensively immersing himself in maker culture and learning as many DIY skills as he can, through a generous arrangement with our pals at TechShop. He’s regularly chronicling his efforts in this column — what he’s learning, who he’s meeting, and what hurdles he’s clearing (um… or not). –Gareth This year marks my first Maker Holiday Season. As I wrote about in my last column, it’s given me an opportunity to reflect on what the last few months have meant. It’s also opened up a whole new world of possibilities: gifts I can make! What I made: A cribbage board shaped like the state of Minnesota (where I’m from). Cribbage is a card game where score is kept on a pegged board. My parents love playing cribbage, and whenever I visit them, it’s my favorite thing to do. I can play my mom and dad in cribbage for hours and not get tired of it. We sneak games in before dinner, in the morning while drinking coffee, or block off a whole night and play. It’s fantastic.  I decided to make them a custom cribbage board. A gift that looked great, would get a lot of use, and highlighted just how much I’ve learned in the past few months. How I made it: I envisioned a number of different designs, but settled on the Minnesota option due to relative ease. I downloaded the vector file of the state online and added all the peg holes to the state outline. Once I had the design I wanted, I had to decide on the material. I thought I might make it out of plastic on the laser cutter, but eventually decided to carve it out of wood on a ShopBot. I’d taken the ShopBot course before but needed a quick refresher on the process. As usual, Zach Johnson at TechShop came to my rescue, helping with the different feeds and speeds and suggesting bits for the different aspects of the project. Zach made some suggestions on router bits – 1/4 inch for the state outline and 1/16 inch to drill the peg holes. Unfortunately, TechShop was out of 1/16 router bits. Zach said he could order one, but it wouldn’t arrive for a few days, and I didn’t have any days to spare until my trip back home. What happened next is something that I’m sure could only happen at a place like TechShop. In a stroke of extremely good luck, Martin Horn overheard Zach’s and my discussion about the 1/16 inch router bit dilemma. Martin, besides being a part-time instructor at TechShop, is a wizard on the CNC machines. Martin said he had an idea that might work – using a custom brass rod to modify a 1/16 inch drill bit. Martin and I took about twenty minutes to try his idea, creating it as he explained it. Pretty soon, we had a part that looked like it just might work – good enough to give it a try, anyways. It ended up working beautifully. The peg holes looked great and the 1/4 router bit was the right endmill for the outline. Thanks to Martin and Zach, I have an great looking gift for my folks. Also, Martin’s makeshift part was an incredible learning experience. What I would have done differently: The cribbage board looks great and my parents are going to love it. However, the project took up a lot of time, and unfortunately, not too many others on my gift list would be thrilled about a Minnesota-shaped cribbage board. Next year, I’ll definitely make all my gifts – it’s awesome! Next time I’m going to make something great, but reproducible – something that everyone I know will love getting. I need to improve my time-investment-to gift-ratio. What I recommend: This year, I’m giving the meta-gift of making. I’m amazed at the incredible deal that TechShop is offering: one month of membership and two free classes for $49! For something that has completely changed my life, I can’t recommend this enough. If you live (or know someone) in the Bay Area, Detroit, or North Carolina, jump on this! Also, I’ve had a chance to look through the MAKE Ultimate Kit Guide and there are a bunch of cool gifts there. The nice part about the Kit Guide is that it rates the difficulty, so you know exactly what you’re getting into. I’ve got my eye on the ArduCopter (if anyone I know is reading this). How you can help me: Please don’t tell my parents what I made them. They don’t read anything I write, so I’m not worried about that, but I’m worried someone is going to foil my plan and forward them this link. Please, don’t be that someone. Happy Holidays! More: Follow David’s Zero to Maker journey My colleagues over on CRAFT all have the work ethics and compulsive tendencies that of any crafter worth his/her stripes. When Rachel and Lish proposed an ornament swap this year, precariously close to Christmas, we all piled on. None of us can resist crafting on a deadline. I whipped up a whole bunch of these cardboard LED robot ornaments on Sunday morning. I used what I had at hand– some cardboard, spray paint, and a whole bunch of LEDs. Since I can’t resist the urge to document my crafts, enjoy this video and see the complete how-to on Make: Projects. Subscribe to the CRAFT Podcast in iTunes, download the m4v video directly, or watch it on YouTube or Vimeo. More:  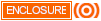  I guess it’s something of an aspirational thing — the desk jockey’s answer to wearing a track suit and never working out — but I’m fascinating by all forms of organizing technologies (while remaining something of a dedicated slob). I have collected all manner of cable management and labeling technologies over the years. The most obvious of this tech is the zip-tie. I use them, but don’t like their permanence. Years ago, a company sent me a big bundle of color-coded Velcro cable ties (that work just like zip-ties, only they’re adjustable/reusable). These have remained my favorite. The only drawback is that the Velcro is very effective and they’re hard to cinch up, and hard to take apart. So I was very interested when I got the PR about the Q Knot reusable rubber ties from a company called UTWire. They work on the same principle as standard plastic zip-ties but they can be fairly easily pulled apart and reused. If you crossed a rubber band with a zip-tie, you’d get a Q Knot. They work similarly to zip-ties except the “gripping teeth” are made of flexible rubber so they can be worked back through the loop end (but the teeth are big enough, the rubber strong enough, that they hold firmly in place under light stress). UTWire sent me one of the Q Knot Pro packs ($9.50 MSRP). It has 25 “Knots” in small (4 3/4″), medium (6″), large (7 1/4″) and in three colors (black, white, green).  The coolest thing about them is that I was able to immediately put the Q Knots to the test. The day they arrived, I started a discussion on my Facebook page about some really ugly blue-cast compact florescent bulbs I had installed in the light by my bedside. This led to a discussion about different types of lighting and someone mentioning LED strip-light material. It just so happened that I had been sent a short test strip of such lighting from a company about six months ago. I grabbed my bag of Q Knots, the LED strip, and the power adapter and headed to my bedroom. Within minutes I had an awesome, perfect reading light set up along the top tube of my iron bedpost. I used two small Q Knots to firmly fix the strip in place and one on the bedpost to secure the power cable. The small dark green rubber ties look unobtrusive and they can be adjusted if need-be. If fact, I moved the strip and wiring several times, something that would have caused me to cut and use new conventional locking zip-ties. I’m really happy with my new bed-light and its use of Q Knots. At first, I thought I’d find a more permanent solution, but I think this is my permanent solution. The only open questions I have about Q Knots are their longevity (think rubber band rot) and their strength. I definitely wouldn’t rely on them to carry a load. The other issue would be, depending on what you’re bundling, how heavy, where you are, etc., wrappin’ these rascals might be a little harder than conventional zip-ties — you really have to put some muscle into cinching them. All-in-all, I’m please with Q Knots. I definitely think I’ll be reaching for them in the future to tie down my life, at least until some shiny-shiny new organizing technology comes along and distracts my flitting bug-brain. More: See all of our “Toolsday” tool reviews here. It’s amazing what a little disk can do … when it’s layered with piezoelectric crystals. Piezo disks are impressively sensitive to vibration and can easily be adapted to work as a contact microphones. The trick is the preamp – a basic circuit used to match the piezo’s signal to levels compatible with modern audio gear inputs. The resulting piezo/preamp combo can be used for electrifying an acoustic guitar or simply exploring the lesser-heard world of small sound around us. 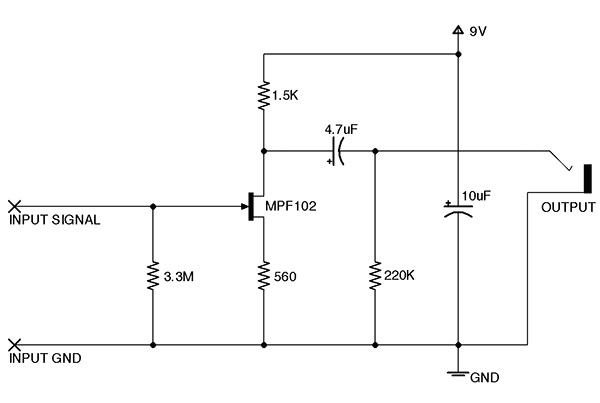 Schematic for piezo preamp The preamp I built is a variation of James T. Hawes’ design. In order to simplify construction, I reversed the MPF102′s source & drain connections from their usual orientation – which works fine in this case. This thing really is an awful lot of fun to play with – you’ll likely here it used in some of my upcoming video soundtracks! Subscribe to the MAKE Podcast in iTunes, download the m4v video directly, or watch it on YouTube and Vimeo. Check out more episodes of Collin’s Lab.  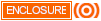 We’re giving away amazing kits from our new Make: Ultimate Kit Guide EVERY DAY — thousands of dollars worth of merchandise, including MakerBots!  To celebrate the release of our latest publication, the Make: Ultimate Kit Guide 2012 (and its companion website), we’re giving away at least one of the cool kits reviewed in the issue each day during the holiday season. Today’s giveaway is for a SAGA S-Style Guitar Kit. Here web ninja Jake Spurlock’s review from the issue (he built the T-Style version): Love to play the guitar, and want to add something custom to your kit? The Saga Electric Guitar Kit offers a blank canvas for guitar building. You could paint it, stain it, or classically distress it to look like your favorite guitar idol. In addition to the guitar body, the headstock has a paddle shape that lets you cut whatever design you want. All of the holes are drilled, and all connections are solderless. The barrier to custom guitar building has dropped, allowing anybody to own a personalized guitar. To be eligible for today's giveaway, all you have to do is leave a comment below in this post. The entry period for today's prize will be until 11:59pm PST tonight. We'll choose one person at random, you'll be notified by email, and you'll have 48 hours to respond. The Winners List is kept on the Giveaway landing page. That's it! No purchase necessary or anything else to do. Please leave only one comment per post. You can enter as many giveaways as you like until you win. This giveaway is for US residents only. You also must be 18 years old to enter (Kids: Ask your parents to enter). See the Kit-A-Day Giveaway landing page for full sweepstakes details and Official Rules. Important Note: If you enter this drawing, when it’s over, please check the place where you registered to comment (eg. Facebook, Yahoo, Twitter) and make sure your profile is visible. Some people are winning these kits and then not responding when we send them a message using the available means of contacting them. We want to make sure you get your giveaway!  Desktop publishing is the established metaphor for desktop manufacturing: A 3D printer is like a paper printer, in that it takes digital information and makes it real. A 3D scanner is like a paper scanner in that it takes real information and makes it digital. From a mechanical perspective, neither a 3D printer nor a 3D scanner is much more complicated than its 2D analog. If, or most likely, when desktop manufacturing takes off among mainstream consumers, 3D printers and scanners may eventually be available at prices on par with paper printers and scanners today. But we’re not there yet. Right now, if you want to get a 3D printer in your workshop for less than $5,000, you’ll be buying it, or the parts for it, from a relatively small company. To save money, you’ll probably be building some or all of the machine yourself, from parts supplied in a kit or sourced independently by you, based on open-source parts lists (though there is usually little to be gained by doing it in this way). Unless you are one of a few intrepid explorers, your hobby-class 3D printer will almost certainly be of the “fused deposition modeling” (FDM) type, in which parts are built up layer-by-layer from a thin bead of molten plastic extruded by a nozzle (or “hot end”) that is, in principle, very much like a hot glue gun. If you’re planning on getting a 3D printer for yourself, the decisions about what to buy, and who buy from, can be daunting. If you’re trying to buy a gift for a 3D printing enthusiast, and don’t necessarily share his or her passion for the subject, the choices can be downright overwhelming, not to mention expensive. Fortunately, there are quality gift options short of buying a whole printer, and we’ve listed some great ones below, from lowest to highest price. On the other hand, if you’re ready to take the plunge and buy a whole printer, our preferred makes and models are listed at the end of the guide, again in order of increasing price. Let’s get to it.  Custom color-printed robot Even among experienced hands, color 3D printing is something of a novelty. The color printing process is a lot like a conventional inkjet printer, except the printhead moves over a bed of finely-divided powder, instead of a piece of paper. And instead of colored ink, it dispenses colored glue. The model is built up, one layer at a time, by gluing together very thin slices, tinted as necessary, where necessary, by a carefully controlled mixture of primary color binders. The clever entrepreneurs at My Robot Nation have capitalized on that process in an entertaining way: Those with no experience in 3D printing will find their browser-based mix-and-match model creation process fun and easy, and those who know their way around 3D printing are still likely to appreciate getting a hands-on look at a relatively unusual technology. You can design the robot yourself, and give it as a gift, or buy a gift certificate so that special someone can design his or her own. For those willing to spend more, MRN offers three larger-sized figures in 1″ increments up to 6″ tall. 3″ Custom Full-Color Printed Robot, $25  3D-printing gift certificates The next step above FDM printing, in terms of technical sophistication, is so-called “selective laser sintering” (SLS), a method in which models are built up, one layer at a time, by a laser beam scanning over a bed of very fine powder. The powder substrates are expensive and messy, and the equipment’s order-of-magnitude improvement in resolution is matched by an order-of-magnitude increase in cost. New cars are a fairly accurate point of comparison: “economy” models cost $10-$20,000, and “luxury” models can run well north of $100K. Fortunately, contract SLS printing is quite accessible these days. The premier online 3D printing contractor is undoubtedly Shapeways, a Dutch firm (now relocated to New York) that has been shipping high-resolution 3D printed models to customers since 2007. Shapeways has a bustling online marketplace, where users can upload and print their own models, or browse and purchase printed copies of models designed by others. Shapeways users can set their own markups for models they design, above material costs and overhead, and skilled designers can make good money from these royalties. Even someone who already has access to a RepRap, MakerBot, or other hobby 3D printer is likely to appreciate a Shapeways gift certificate, because Shapeways’ printers can do things that hobby-class printers cannot, such as printing at 0.2mm resolution and/or in exotic materials like ceramic, sterling silver, and stainless steel.  Digital fabrication gift certificates New Zealand-based Ponoko, also launched in 2007, competes with Shapeways, to some extent, to provide contract SLS printing services. Their business model is very similar, with an online marketplace where users share designs and profit from sales of goods manufactured on demand. Ponoko does not offer as many 3D printing materials as Shapeways, but unlike Shapeways, they provide a range of other computer-controlled manufacturing processes besides 3D printing, including laser-cutting and CNC routing, as well as an inventory of common fasteners, electronics components, and other hardware that can be mixed-and-matched to create complex custom products. Though Ponoko goes to great lengths to make their system as simple and user-friendly as possible, the greater number of processes and materials they provide, and the vastly greater number of ways that those processes and materials can be combined, makes for a slightly steeper learning curve. On the other hand, for a person looking to explore what the field of digital fabrication has to offer in a more general way, a dollar to spend at Ponoko has a lot more potential than a dollar to spend at Shapeways. Ponoko gift voucher, $10 / $25 / $50 / $100  3D modeling guides A person interested in 3D printing is, almost necessarily, also going to be interested in making and manipulating 3D models, and for that he or she will need software. One of the most exciting things about 3D modeling today is how many great programs are available, for free, and —though opinions may differ on this point—a hobbyist designing models for desktop FDM printing is unlikely to ever really need to buy “professional” 3D modeling software at all. Exactly which of the many freely-available 3D modeling programs is best will vary with what’s being modeled, how the model’s going to be used, and the personal preferences of the modeler. In my experience, three programs stand out: SketchUp, Blender, and OpenSCAD. Google SketchUp, which since version 7.1, has included the ability to export directly to .STL format (even in the free version), is best for small CAD-type projects involving parts with precise dimensions and not too many compound curves. Blender, on the other hand, is better for “sculpting” — making character art or other models with complex curves and surfaces that are shaped intuitively by eye and/or by “feel.” Finally, there’s OpenSCAD, which eschews the what-you-see-is-what-you-get interface in favor of a programmer’s “development environment” in which models are literally scripted, instead of sculpted. OpenSCAD is my choice when the subject admits of mathematically precise modeling, constructive solid geometry (CSG), or parameterization. All of these programs require some experience and/or training to use effectively. Of the three, SketchUp is probably the most intuitive, for simple models, but it can quickly become a real pain if you have to actually manipulate the mesh. Blender, on the other hand, has a somewhat notorious learning curve, but is hugely powerful once you become proficient. Users of either program will benefit from a good manual, and O’Reilly has one of each. I can personally vouch for Roland Hess’s The Essential Blender, which got me over the hump nicely. As for OpenSCAD, as far as I know, to date there are only the wiki, the odd tutorial, and an official mailing list to help educate new users. An opportunity for an aspiring technical writer, perhaps? Google SketchUp: The Missing Manual, $35 print / $28 digital The Essential Blender, $45  RepStrap parts If you buy a modern 3D printer kit, some of the parts you receive will probably have been printed, themselves, on a machine identical or closely related to the one you’re building. The open source RepRap project, which is the spiritual and technical progenitor of pretty much every commercial hobby-class 3D printer going, has from the beginning worked towards a design capable of complete self-replication. Again, we’re not there yet, but RepRap’s most popular iteration, the Prusa Mendel, has reduced the need for commercially-manufactured parts (or “vitamins,” as they’re sometimes called) to a truly remarkable extent. A RepRap, essentially by definition, is mostly made of parts printed on another RepRap. It is possible, of course, to build a 3D printer based on a RepRap design using parts manufactured by other means, and such a machine is often called a “RepStrap.” The hackers of Seattle’s Metrix Create: Space have pioneered a RepStrap technique using parts cast in resin in 3D printed molds. Perhaps because parts thus produced are radically cheaper than parts actually printed on a RepRap, the “Clonedel” project as it’s known, has met with some controversy in the community. Back in March, however, Neil Underwood reviewed them favorably on the official RepRap blog: 18 Months ago the plastic parts for a Mendel where going for $700+, 12 Months ago the price settled down to $250-$400, 3 Months Ago Prusa Mendel dropped the price for the RP parts to $125-$150. Now the Clonedel cast RP parts are going for $50 (I personally know of three shops gearing up to start selling them). I wrote a post over at my personal blog a few weeks ago describing how to put a Prusa Mendel together if you don’t have access to a 3D printer for around $510. I guess I need to update it to $410 now. Amazing times. Clonedel Part Set, $50  3D scanner parts In desktop manufacturing, as in desktop publishing, scanning is the Yin to printing’s Yang. Along with modeling from scratch, scanning — in which a real 3D object is imaged to produce a virtual 3D representation — is the other major method for making 3D models, which can then be manipulated in software and/or printed as necessary. Commercial 3D scanners are available. See, for instance, the NextEngine Laser Scanner below which is at the low end of the field at $3,000. Depending on configuration and options, however, “professional” 3D scanners can be as expensive as professional 3D printers, or even moreso. Fortunately, it is easy, almost astoundingly so, to build DIY 3D scanners capable of very impressive results. There are two common methods, but both involve capturing digital images of a subject under illumination with patterned light, and then analyzing those images, in software, to extract a shape. A technique known as “structured light scanning,” popularized by Kyle McDonald in this 2009 Instructable, combines a video projector and a digital camera with an open-source software package called ThreePhase to produce a low-cost DIY 3D scanning system that does not require a backdrop for calibration. Structured light scanning was famously used to produce the point clouds in Radiohead’s 2008 House of Cards video. For the method to work well, projector and camera need to be rigidly mounted in relation to one another, and the good folks at MakerBot have put together this laser-cut plywood enclosure, sold as a kit with all the necessary hardware, to serve that purpose. The pocket video projector is mounted in the center of the cube, and the digital camera on top. MakerBot maintains a 3D Scanner wiki about how to put together a structured light scanning system using the frame, including details of what hardware and software work best. MakerBot 3D Scanner Mounting Kit, $73  Micro video projector Quite apart from its other potentially awesome uses, like building a spherical display or a homebrew stereolithography printer, a “pocket” or “pico” video projector is an integral part of a structured light scanning system. These tiny projectors use LEDs or lasers for illumination, instead of incandescent bulbs, and though the MakerBot 3D scanner wiki recommends the LED-based Optoma Pico and AAXA Ultra Pico Jr, I would have a hard time turning down the laser-based MicroVision models, which are now available for about the same price. The laser models will be much brighter and have better resolution, to boot. Note that if you don’t want to use an iDevice to run the projector, you may need to purchase a converter so you can plug a standard VGA out into one of these tiny devices. Shown in the picture is MicroVision’s top-of-the-line model, which has a handy compact HDMI input. AAXA P1 Jr Ultra Portable Pico Pocket Projector, $108 Optoma EP-PK-101 Pico Pocket Projector, $125 MicroVision SHOWWX Classic Laser Pico Projector for iPod, $135 MicroVision SHOWWX+ Laser Pocket Projector, $300 Microvision SHOWWX+ HDMI Laser Pico Projector, $370  3D scanning software The other common DIY 3D scanning technique, and the first to make a big splash on the web back in 2006, involves using a laser line generator, instead of a video projector, to illuminate the subject. This method typically requires a white 90-degree corner backdrop printed with a special black calibration pattern, but has the advantage of not requiring a video projector. The backdrop is not difficult to prepare and laser line generators are likewise inexpensive to buy and/or easy to make. (One popular tutorial improvises a line generator from a laser pointer and a wine glass stem, for instance.) With the subject in place before the backdrop, one simply turns off the lights, turns on the camera, and “paints” the subject with the laser line, by hand, from a variety of angles. The magic software does the rest. And though it is possible to use MATLAB, for instance, to extract point clouds from raw image data gathered this way, the folks at Germany’s DAVID Vision Systems pioneered this technique, back in 2006, and have been continuously developing their application-specific software since then. DAVID Laserscanner generates 3D data in real time and allows you to watch, on the scanning computer screen, how the model is developing as you work. It can stitch together scans of the same object taken from multiple angles, and exports directly to STL, OBJ, and other popular 3D file formats. The latest versions have added support for no-backdrop structured light scanning using a video projector, as well as traditional laser line scanning. Best of all, you can try it out for free with the trial version, which has some restricted options and a scan resolution cap, but is otherwise fully functional. DAVID-Laserscanner Pro Edition 3.x Upgrade Code, $150  Prusa Mendel Kit Thanks to Pete Prodoehl for this sublimely elegant photo of a sublimely elegant machine. From RepRapWiki: Prusa Mendel is the Ford Model T of 3D printers. Like the Model T, the Prusa Mendel improves on a previous design by being more streamlined for manufacture. The Prusa Mendel is a simpler remix of the original Mendel. Prusa’s main goal is to be the purest and simplest 3D printer you can build. It’s much simpler to build it. It’s much simpler to modify it. It’s much simpler to print it for your friends. It’s much simpler to repair it. Many people are making and selling Prusa Mendel kits. For an extended list, see the official RepRap Buyer’s Guide. My own tremendously positive experience with Rick and Karen Pollack’s MakerGear Mosaic has convinced me to endorse their Prusa Mendel kit, here. But you don’t have to take my word for it: Check out the glowing reviews. Prusa 3D Printer, $850  The MakerGear Mosaic I will admit to being slightly biased toward the MakerGear Mosaic. I am now most of the way through building my own, and as I have often joked in my weekly build guides, I keep waiting to get to the difficult part. I planned for seven weeks to complete all seven parts of the guide, but in fact, that has proved an extreme overestimate of the time the actual build would require. My progress is slowed by the requirement to get good photos of every step, but even so I think I will end up spending about seven hours, altogether, in its construction. All the complicated subassemblies are pre-built and come out of the box ready to drop in place. I haven’t got it printing yet, so there’s always the possibility of a last-minute surprise or two. But so far, “smooth sailing” is putting it mildly. Mosaic 3D Printer, $1,000 kit / $1,500 assembled 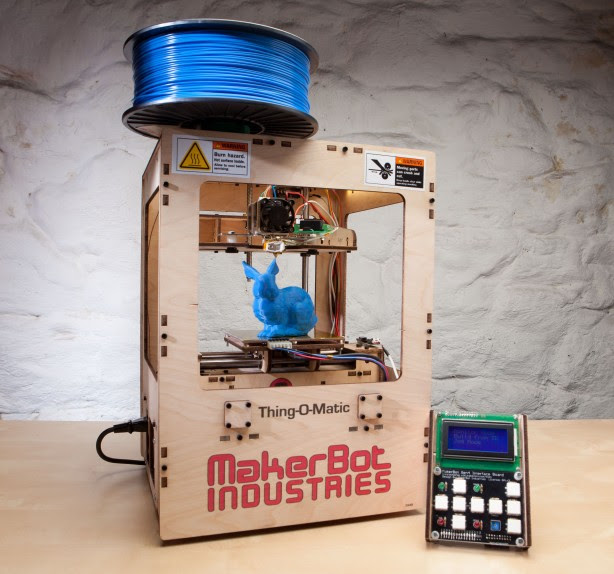  The MakerBot Thing-O-Matic This device may look familiar to you. That may be because we’ve been giving them away like Halloween candy over the past couple of weeks. Or perhaps, you may recall, back in August, having seen it on television printing a copy of Stephen Colbert’s head, or more recently, in September, in a beautiful full-page exploded view in The New York Times. Then again, maybe you just recently noticed it on the cover of your copy of the Make: Ultimate Kit Guide. Here's Make: Labs intern Eric Chu's review of Thing-O-Matic from that issue: If you want to get into 3D printing but don't know where to start, the MakerBot Thing-O-Matic Kit is the way to go. It's a complete kit, so you need no additional parts, and a large user community can back you up if problems pop up (not to mention Thingiverse, where you can find awesome open source designs). It took me about 20 hours to build the Thing-O-Matic and start printing, and I improved its accuracy with more tuning, calibrating, and tinkering with settings in the ReplicatorG software. If you have any trouble, read the discussion at the bottom of every build step. I've since 3D-printed many fun and handy things (everyone loves a 3D-printed gift!) and the MakerBot is now by far the most-used machine at Make: Labs. MakerBot Thing-O-Matic Kit w/ Stepstruder MK7, $1,100 Custom Fully Assembled MakerBot Thing-O-Matic, $2,400  Entry-level business class 3D scanner If you believe the hype, the NextEngine 3D Laser Scanner represents both a big leap forward in quality, and a dramatic reduction in price, in the “professional” 3D scanner market. Though it’s included here, like the ZPrinter 150 below, mostly to establish a point of reference for the cost of the cheaper DIY alternatives, the NextEngine does make some intriguing claims: Full color scanning, up to 0.005 inch accuracy and 400 data points per square inch, two minute capture times, and no inherent size limitations (besides field-of-view) on scanned objects. They’ve even got Jay Leno endorsing the thing. NextEngine 3D Laser Scanner HD, $3,000  Entry-level business class 3D printer Finally, there’s pro-grade 3D-printing equipment. Boston’s Z Corporation has an established reputation as a leading manufacturer of high-end rapid prototyping machines as well as “entry level” gear which, though still inaccessible to most hobbyists, is within the grasp of many small businesses. The ZPrinter 150, shown here, is their least-expensive 3D printer offering, and is included mostly to provide a point of comparison. If you can afford to give one as a gift, though, more power to you. And by the way, would you like to be friends? ZPrinter 150, $15,000 SPONSORED CONTENT When I talk to non-geeks about 3D printing, they’re amazed that such a technology exists today, they joke about needing one now, and then they ask when a consumer out-of-the-box 3D printer will be available. That’s what the UP! Start Plus v1.1 bills itself as: "the first assembled, all-metal, portable, consumer friendly 3D Printer that is ready to print in about 15 minutes out of the box." -Gareth  The UP! USA Store @ www.up3Dusa.com is offering a deal through Dec 31, 2011. For $2,250.00 (plus $85.00 S&H) you will receive their UP! Start Plus v1.1 printer, (1) spool of white ABS (0.7kg), a platform perfboard kit, a tool and accessories kit, and UP! Software for PC and Mac OS. Here are some highlights of the UP! Start Plus: - Uses 1.75mm ABS & 1.75mm PLA materials
- High-resolution, precision printing at 0.20mm Z layer resolution
- Build Volume: 140mm(w), 140mm(d), 135mm(h) – 5-1/2″(w) x 5-1/2″(d) x 5-1/4″(h)
- Heated, metal build platform integrated with & controlled by UP! software and mainboard electronics.
- USB connectivity to mainboard and internal 2G SD card memory
- Software included by download. Allows importing of .STL files, manipulation and preparation of model for printing on the UP! Automatically generates necessary custom support structure for each build
- Overall Dimension: 245mm(w), 260mm(d), 350mm(h), 9- 5/8″(w), 10-1/4″(d), 13-3/4″(h)
More: Check out all of our MAKE Holiday Guides and Programs 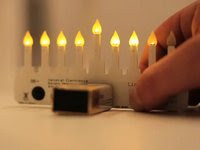 I’m not Jewish but if I were I would definitely have one of these LED Menorahs, available in the Maker Shed, on my desk. The Hanukkah Electronica (above) is an elegant, pre-assembled LED Menorah for celebrating the festival of lights. The simple, elegant design uses a 9v battery (included) as a stand. The push button on the back allows you to burn whichever lights you desire. The flickering of the LEDs gives the Menorah a memorizing, warm glow. It’s an easily transportable, pocket sized work of art that will have everyone wanting to celebrate Hanukkah. 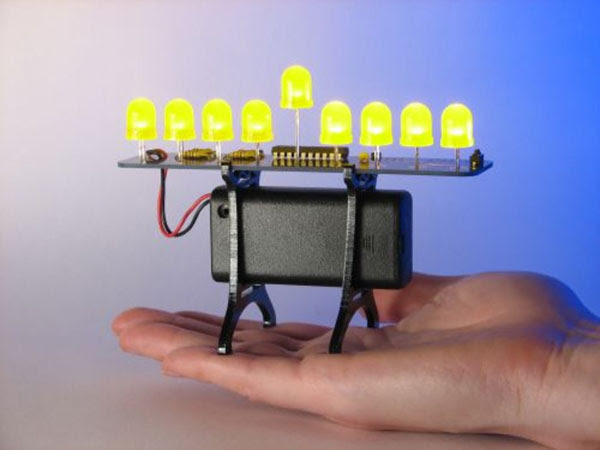 The Deluxe LED Menorah Kit is an updated take on the traditional hanukkiyah, the nine-armed Hanukkah candelabrum. When you turn it on, it displays the correct configuration of LED “candles” for a given night of Hanukkah. Each time you press the button (or switch it off and back on), it displays one more light (unless it showed all nine last time, in which case it goes back to two). The LEDs are lit up in the traditional sequence, with a gentle fade. This kit is very easy to build, and includes a preprogrammed microcontroller, battery holder, nine ultrabright, 10mm LEDs, an alignment guide for the LEDs, and a laser-cut acrylic stand. Once you’ve built it you’ll have an elegant little LED menorah ready for the season. | |
No comments:
Post a Comment
Keep a civil tongue.